Hydraulic
Platen Press:
Click Here For Our Latest Hydraulic Press News !!
Many
of the press designs used in the composite industry were taken from
plywood presses. Although these presses can produce many of the
composite products they fall short on many technical requirements
needed for superior physical performance on a variety of composite
parts. SDM addressed many of these factors to produce a better press.
These improvements include:
- Load
distribution over the platens
- Temperature
uniformity
- Temperature
gradients as temperature transitions to higher or lower range
- Platen
stability under heavy pressure.
All of these areas were addressed to optimize processing of difficult
resin systems. Pressure uniformity surveys verify bolster rigidity,
platen stability and carrier bolster load uniformity.
SDM
delivered its first Dual Loader LAMINATOR SERIES production
press in April 2000. This press, a 5 Ft x 12 Ft, allows loading
from the front or sides. With this feature, 5 Ft x 24 Ft panels
can be produced with one step. This flexible design opens a wide
variety of manufacturing options. Large California freeway
signs are currently produced with this equipment.
With our MAX RAMP feature new levels of uniformity
and temperature rate changes have been incorporated into the LAMINATOR
SERIES of presses. These presses offer unrivaled temperature
uniformity and are capable of temperature rise rates of 20°F
/ per minute while maintaining excellent platen uniformity. This
feature can enhance the physical performance of phenolic faced honeycomb
panels, and other resin systems.
Our features deliver:
- High
quality, high performance honeycomb structures
- Eliminates
weakened areas, unseen and difficult to detect by inspection.
(NDT will NOT show these flaws).
- Uniform
physical strengths throughout the panel
- Dramatically
reduces loss rates in panel processing
- Typically
reduces cycle times for more efficient production
- Short
gel times can be processed into quality parts.
Platens are heat treated structural steel for stabilization during
thermal changes. They are blanchard ground, flat and parallel within
0.004". For the highest quality, the platens are gun
drilled in house at SDM. All fittings are forged steel
including the valves. Hoses are stainless steel 300 PSI and 600°F
Service. The heat transfer pump is also rated at 600°F to assure
long life. The hydraulic power pack is an air over oil system that
is quiet and efficient. The heater has a fully modulated burner
with full controls and high limit safety.
Additionally:
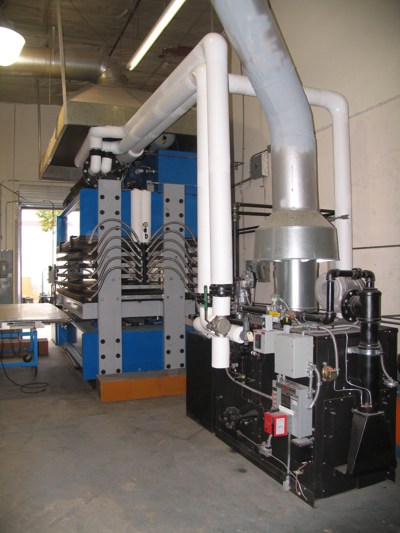 |
Shown is a Stage I Cooling System
with a SDM 450 Ton Platen Press |
- The
massive upper bolster is designed for minimum deflection under
maximum load
- The
center carrier uniformly distributes the cylinder loads to the
platens
- The
hydraulic cylinders are custom made by Eaton for SDM. Eaton
cylinders are the highest quality cylinders in the industry.
- SDM/Eaton
cylinders feature an extra large rod diameter to reduce leakage
and stabilize deck travel. They have 3000 PSI continuous and 5000
PSI intermittent duty rating. The result is a virtually maintenance
free press that will produce the highest quality composites from
a wide variety of materials.
Super Cooling:
SDM super cooling systems support our laminator series of presses and come in 3 different cooling stages.
The exchanger with this system has a service temperature of 40°F to 450°F to handle the processing requirements for the cooling system.
- Stage I - Is a self contained unit, typically placed on top of the press. These cooling units are excellent for the process of manufacturing
phenolic faced nomex(tm) interior panels and can typically cool a press from 250°F to 200°F in 45 minutes for multiple cycles per day.
- Stage II - Improves on the Stage I features by adding a cooling tower allowing even greater capacity and shorter process times.
- Stage III - Dual Stage Super Cooler Is the most aggressive cooling system we offer. This Super Cooler adds a specialized refrigeration loop for a dual stage
process. Stage III units are capable of cooling our SDM presses from 320°F to 180°F in 45 minutes depending on the design chosen.
Who Relys on SDM Presses?
Nordam Industries, J.D. Lincoln, M.C. Gill, AAR Composites, Teklam, Paneltech, Driessen Aerospace and Advanced Composites are just a few of our clients that have incorporated an SDM Technology Press into their production processes. Click
Here
for our IN-STOCK Inventory of LAMINATOR SERIES presses
available to immediate sale.
Contact
SDM for Further Information and a Quote!
|